Автоматическая выхлопная труба, напечатанная на 3D-принтере по металлу Eplus3D EP-M250
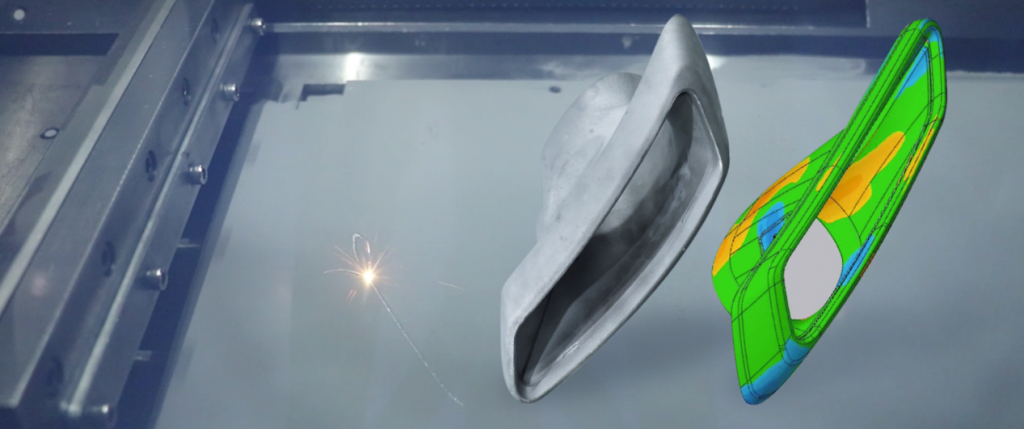
История:
При использовании традиционного метода производства на изготовление первого автомобиля с завода обычно уходит почти 3 года. В то время как аддитивное производство выгодно не только из-за сокращения времени проектирования и производства, но и из-за создания деталей сложной конструкции. В последние годы большинство известных автомобильных брендов, таких как BMW, Audi и Volkswagen, создали центры аддитивного производства, чтобы интегрировать новые технологии в свой производственный процесс.
Вступление:
Eplus3D тесно сотрудничает с автомобильными компаниями и командами гоночных автомобилей, чтобы помочь им внедрить аддитивное производство с целью повышения производительности и снижения затрат. Один из недавних случаев - помощь компании в разработке, производстве и испытании выхлопной трубы для автомобиля на новом этапе разработки продукта с использованием технологии MPBFTM Eplus3D и высокоточной технологии 3D-сканирования и контроля в синем свете.
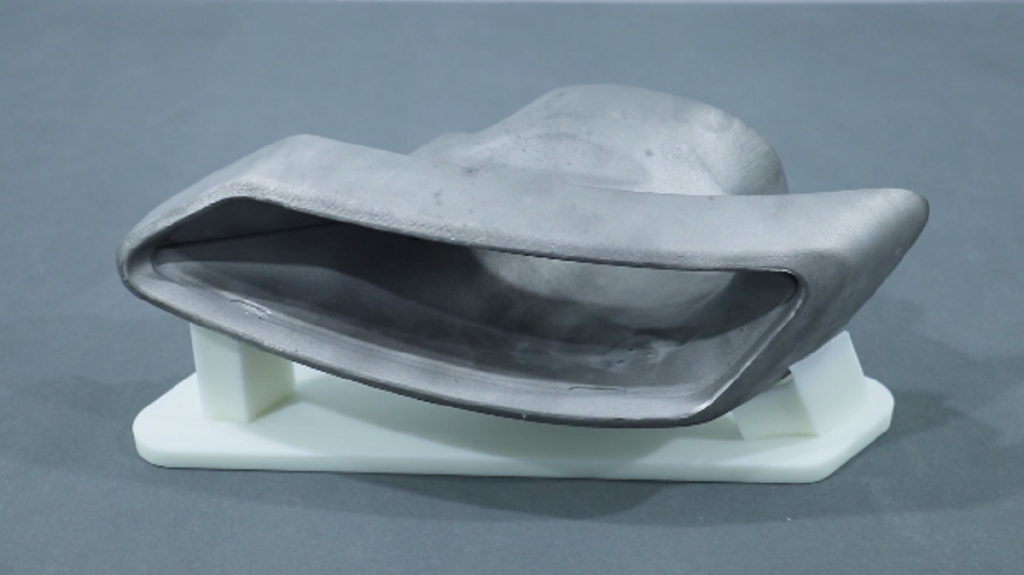
От 3D-печати до 3D-инспекции:
Для просмотра видео в реальном времени перейдите по следующей ссылке:
https://www.youtube.com/watch?v = HaK-Ola5OZgЗаключение:
За счет применения подхода аддитивного производства и трехмерного контроля период от проектирования до установки сократился до одной недели, что привело к значительному сокращению времени производства, рисков и затрат. Дополнительные преимущества инновационных технологий обеспечивают новый, легкий дизайн с большей свободой, отвечающий растущим индивидуальным требованиям автомобильной промышленности. Без сомнения, аддитивное производство будет играть гораздо более важную роль в будущем, Eplus3D разрабатывает технологии прямой печати, серийного производства деталей по индивидуальному заказу и изготовления более крупных деталей для более широкого круга приложений.