В последние годы стоимость производства АП для усовершенствованных материалов постоянно растет, чтобы обеспечить производство специальных порошков для аэрокосмической, национальной обороны и биомедицинских приложений.
Понять разницу в поведении порошка при деградации
Различные типы порошков будут демонстрировать разные изменения производительности после одного или нескольких циклов печати. Inconel 718 обладает химической стабильностью в процессе переработки, но при оценке возможности повторного использования она ограничена физическими свойствами, такими как форма и текучесть. Когда эти материалы плавятся при более высоких температурах, материал вокруг расплава деформируется и спекается вместе, что делает частицы порошка больше и непригодны для использования. Порошок титанового сплава легче абсорбирует кислород, и чем выше содержание кислорода в порошке, тем хуже печать. Поэтому необходимо постоянно обращать внимание на окисление порошка, и время его использования будет значительно ограничено.
Понимание поведения различных порошков при деградации важно для разработки стандартов вторичной переработки порошков.
Деградация металлического порошка после многократного использования
В исследовании восстанавливаемости высокотемпературных материалов порошок из нескольких циклов печати был проанализирован, чтобы понять влияние на характеристики порошка и деталей. В процессе многопечати сателлитный порошок, прикрепленный к более крупным частицам порошка, начал отделяться и образовывать более мелкие одиночные частицы. В то же время частицы порошка начали плавиться с образованием агрегатов, и частицы агрегата распались на неполные мелкие частицы. Все это влияет на текучесть и объемную плотность порошка, делая гранулометрический состав порошка шире и увеличивая содержание кислорода в порошке. Однако после использования одной и той же партии порошка в течение 13 последовательных циклов порошок по-прежнему соответствовал спецификации состава и требованиям повторного использования.
Два метода повышения скорости переработки порошка
Чтобы улучшить возможность повторного использования металлического порошка, необходимо определить квалифицированные технологии для ремонта неквалифицированного порошка и сделать его многоразовым. Популярный метод - смешивать новый порошок со старым перед каждой сборкой. Он может снизить содержание кислорода в порошке и отрегулировать физические свойства, такие как гранулометрический состав и насыпная плотность порошка, но не существует установленного стандарта смешивания, поэтому пользователи полагаются на свой опыт для определения оптимального соотношения. Эти попытки часто варьируются в зависимости от используемого материала и типа производимых деталей.
Другой разумной технологией ремонта является технология индукционной плазмы, которая отправляет порошок неправильной формы и плохой текучести в индукционную плазму, быстро нагревается и плавится при высокой температуре с образованием капель, которые собираются в шар под действием поверхностного натяжения и затвердевают. при падении с получением сферических частиц порошка.
Сравнение до и после обработки индукционной плазмой
При повторном плавлении и отверждении частиц порошка пористость уменьшается, а плотность порошка увеличивается. Увеличивая температуру плавления плазмы и модифицируя защитный газ, можно выборочно удалять примеси для повышения чистоты порошка. EWI, научно-исследовательский институт, провел несколько ранних исследований с использованием этого метода, но перед оценкой возможности ремонта порошком необходимо провести дополнительные испытания.
Разработать отраслевые рекомендации для улучшения прослеживаемости
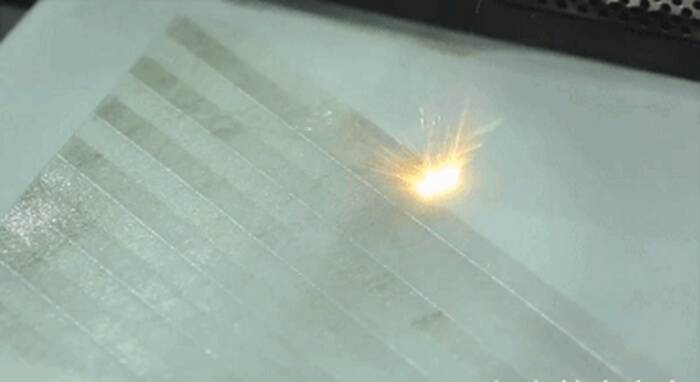
По технологии порошкового ремонта предстоит еще много работы. Например, хотя смешивание старого и нового порошков может снизить общее содержание кислорода в порошке, порошок все еще содержит частицы с высоким содержанием кислорода. Если эти частицы, наконец, попадут в деталь, это приведет к ее катастрофическому выходу из строя. Некоторые исследования показали, что более высокое содержание кислорода в порошке Ti6Al4V приводит к снижению прочности деталей на разрыв.