Дизайн и производство легких компонентов - иногда называемых легковесными - является растущей тенденцией во все большем числе отраслей, включая транспорт, производство инструментов, энергетику и здравоохранение.
Как следует из названия, облегчение - это процесс создания более легких компонентов при сохранении или даже увеличении их целостности и прочности. Некоторые из преимуществ включают:
- Более легкие компоненты предлагают широкий спектр преимуществ от повышения топливной эффективности при транспортировке до большей жизнеспособности в качестве имплантатов или протезов.
- Компоненты часто по крайней мере такие же прочные, как и ранее использовавшиеся тяжелые материалы, благодаря технологическим разработкам и улучшениям коммерческой осуществимости.
- Более эффективное использование материалов и энергии, необходимых для производства, что делает их более экологически чистыми и снимает растущую озабоченность как политиков, так и потребителей.
- Снижение цены. Меньше материала на компонент означает меньше капитала на компонент.
Аддитивное производство помогает преодолеть многие препятствия на пути производства легких компонентов. Вот четыре способа, которыми аддитивное производство / 3D-печать помогает производить более легкие компоненты:
Метод I – Решетчатая структура
Аддитивное производство делает использование и масштабирование решетчатых структур гораздо более доступным.
Вы можете этого не осознавать, но повсюду можно увидеть решетчатые конструкции (мосты, Эйфелеву башню) и даже в природе. Решетчатые конструкции отличаются высоким удельным весом.
Решетчатая структура представляют собой трехмерные структуры с открытыми ячейками, состоящие из одной или нескольких повторяющихся элементарных ячеек. Эти ячейки определяются своими размерами и связью составляющих их стоек, которые соединяются в определенных узлах и могут достичь идеального баланса инженерной прочности, ударной вязкости, долговечности, статики, динамики и стоимости производства.
Относительная плотность кристаллической решетки, форма, размер и материал регулируются путем периодического дублирования большого количества отдельных ячеек для проектирования и изготовления, чтобы регулировать механические свойства структуры, такие как прочность и ударная вязкость.
Трехмерная решетчатая структура обеспечивает высокую степень пространственной симметрии, которая может равномерно распределять внешнюю нагрузку, уменьшать вес и увеличивать несущую способность. Помимо инженерных приложений, полая решетчатая структура имеет «зазор» (или регулируемое отверстие), который может облегчить интеграцию в тело человека и ткань имплантата при наложении имплантата.
Решетчатой дизайн очень гибкая, и элементы решетки различной формы, размера и пористости могут быть адаптированы к их использованию. В области с высокой структурной прочностью плотность элемента решетки может быть увеличена, и можно выбрать полый элемент решетки с высокой структурной прочностью.
В области с высокими требованиями к снижению веса компонента может быть добавлена полая решетчатая структура с большим диапазоном снижения веса. Полая структура может располагаться равномерно или беспорядочно с образованием пор неправильной формы. Кроме того, полая структура также может иметь градиентное переходное устройство переменной плотности и толщины для удовлетворения требований общей градиентной прочности компонентов.
Метод II - Проектирование полых прослоек / тонкостенных конструкций с жесткой структурой
3D-печать дает дизайнеру широкий спектр возможностей дизайна, недоступных традиционным процессам.
Использование различных заполнений (прослоек), настроек и толщины стенок позволяет проектировщику не только уменьшить чистый вес компонента, но и компенсировать различные нагрузки и напряжения, которые компонент должен будет нести.
Заполненная структура помогает снизить вес компонентов. Он обеспечивает хорошее рассеивание внешнего давления, а тонкостенная структура (например, толщина стенки менее 1 мм) способствует снижению веса.
Рассмотрим простой карниз для штор, подверженный изгибающей или изгибающей нагрузке, когда материал поверхности принимает на себя большую часть растягивающих и сжимающих напряжений. Теперь представьте заполнение керна, которое было добавлено, чтобы помочь распределить нагрузку. Эффект будет заключаться в увеличении общей прочности стержня без использования твердого металлического стержня или даже без увеличения толщины стенки.
Кроме того, в радиаторах можно использовать заполнители и другие подобные конструкции, чтобы улучшить площадь теплообмена и эффективность рассеивания тепла деталями.
Таким образом, межслойная структура имеет преимущества, заключающиеся в снижении веса нетто, высокой жесткости и прочности на изгиб, сильной устойчивости к нестабильности, сопротивлении усталости, звукопоглощению и теплоизоляции.
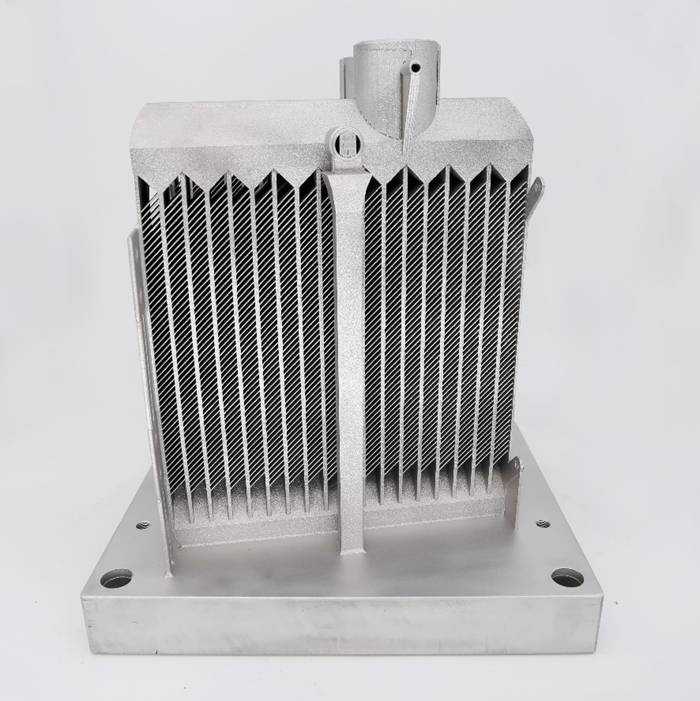
В авиации, лопастях ветряных турбин, кораблях, поездах и других областях для снижения веса широко используются легкие межслойные конструкции.
Метод III - Топологическая оптимизация
3D-печать - самый эффективный метод оптимизации топологии.
Оптимизация топологии - это математический метод, используемый для выявления и удаления лишних материалов, которые не влияют на функциональность детали, путем определения оптимального распределения материала в пределах требуемых параметров.
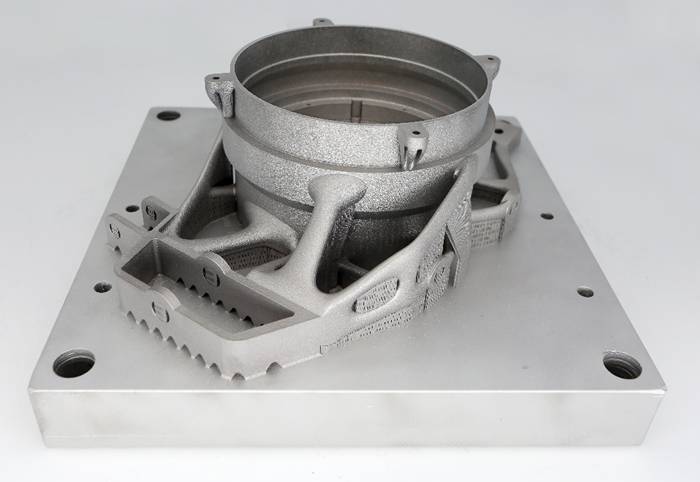
После оптимизации топологии структура особой формы моделируется и анализируется для завершения окончательного моделирования. Нет ничего необычного в том, что оптимизированные компоненты легче более чем на 45%, чем их неоптимизированные аналоги.
Иногда эти проекты могут быть созданы с использованием традиционных методов, но традиционные методы не позволяют реализовать всю ценность процесса оптимизации. Например, 5-осевой фрезерный станок с ЧПУ можно использовать для уменьшения веса нетто и достижения желаемой топологии, но только путем производства эквивалентного количества отходов.
С другой стороны, аддитивный процесс 3D-печати исключает (или, по крайней мере, значительно сокращает в случае опор) ненужные материалы и обеспечивает полную эффективность процесса оптимизации.
Метод IV - Интегрированные компоненты
3D-печать может использоваться для производства интегрированных деталей, изначально состоящих из нескольких компонентов в один. Этот процесс не только улучшает целостную структуру всей конструкции, но также позволяет избежать использования соединительных конструкций, таких как фланцы, сварные швы и т. Д., Используемых в исходной конфигурации деталей.
Это помогает дизайнерам преодолеть ограничения и реализовать функциональную оптимизацию дизайна.
Интегрированная структура с помощью 3D-печати не только снижает тенденцию к перегреву сопла и отложению углерода, но также увеличивает срок службы сопла и улучшает характеристики двигателя.
Вышеупомянутые четыре конструкции для 3D-печати являются одним из направлений реализации облегчения механической обработки, и это систематический проект. От оптимизации конструкции и производства каждого ключевого компонента до исследований, разработок и применения легких материалов, он незаменим на пути легких исследований.